Welcome to the Onshape forum! Ask questions and join in the discussions about everything Onshape.
First time visiting? Here are some places to start:- Looking for a certain topic? Check out the categories filter or use Search (upper right).
- Need support? Ask a question to our Community Support category.
- Please submit support tickets for bugs but you can request improvements in the Product Feedback category.
- Be respectful, on topic and if you see a problem, Flag it.
If you would like to contact our Community Manager personally, feel free to send a private message or an email.
Mate motion propagation/inherit through assembly levels
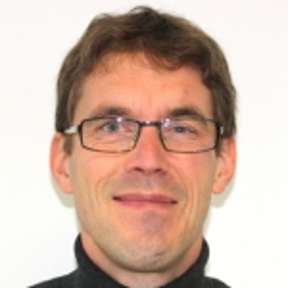
I have the following assembly structure
Top-Assembly
Sub-Assembly 1 (stationary)
Sub-Assembly 2 (rotating relatively to Sub-Assembly 1)
With Sub-Assembly 2 having the following structure
Sub-Assembly 2
Sub-Assembly 3 (stationary)
Sub-Assembly 4 (sliding relatively to Sub-Assembly 3)
Now on top-Assembly level I have one revolution mate, so that Sub-A2 can rotate around Sub-A1 (0°-90°).
This is the motion when the Assembly is moved from its parking position to its working position.
Once in the working position only the slider should move up and down.
With my structure I believed I could "isolate" the motions, as the slider is "contained" in Sub-A2
But when I rotate it (animate), also the slider mate moves simultaneously.
Only with temporarily fixing a part of Sub-A2 in the desired position I can move/animate the slider with out rotating the whole sub-a2
Is there a better way to model it?
Or how are the mate laws inherited in the structure?
I wanted to attach a video but do not know how that works.
but I might share the document/assembly if someone likes to help.
Top-Assembly
Sub-Assembly 1 (stationary)
Sub-Assembly 2 (rotating relatively to Sub-Assembly 1)
With Sub-Assembly 2 having the following structure
Sub-Assembly 2
Sub-Assembly 3 (stationary)
Sub-Assembly 4 (sliding relatively to Sub-Assembly 3)
Now on top-Assembly level I have one revolution mate, so that Sub-A2 can rotate around Sub-A1 (0°-90°).
This is the motion when the Assembly is moved from its parking position to its working position.
Once in the working position only the slider should move up and down.
With my structure I believed I could "isolate" the motions, as the slider is "contained" in Sub-A2
But when I rotate it (animate), also the slider mate moves simultaneously.
Only with temporarily fixing a part of Sub-A2 in the desired position I can move/animate the slider with out rotating the whole sub-a2
Is there a better way to model it?
Or how are the mate laws inherited in the structure?
I wanted to attach a video but do not know how that works.
but I might share the document/assembly if someone likes to help.
Tagged:
0
Best Answer
-
john_mcclary Member, Developers Posts: 3,959 PRO
For those following along, here is what we came up with as a solution:
He only wants to move the pivot arm (shown at 45°) for tool change over
and the purple linkage arm is a separate and continuous animation during machine operation.
because the rotation of the pivot arm changes the XYZ location of the purple arm. The rotation value of the purple also needed to increase by 90° while the pivot arm made it's motion.
because he only needs one at a time, we just made a couple of temporary locking mates to keep things in check.
he will just need to toggle between them depending on which he wants to move.
(would be easier if there were an assembly configuration checkbox... ahem)
6
Answers
But I do know sub assembly mates can be tricky sometimes. Especially if you have more than one part fixed, or misuse group mates.
I'm trying to picture what the animation "should" look like vs what you are actually getting.
Please let me know how I can share the document with you. I guess I need your email address to share the document only with you (individuals tab)
I tried typing your name but it was not auto-filled in then...
I am located in Switzerland, due to the timezone I can not promise I am still there in case we want to do a small websession explaining the case.
Here are 2 pictures explaining shortly the problem:
When I drag the sub-assembly (1) "Schneide Schwenkteil" as arrow (2) indicates, it shoud rotate around bearing point (3) as the top-assembly Mate "Schwenken" defines. The carriage 4 should not move during the drag (but it currently does)...
On the other hand: once the sub-assembly is in the working position, animating the crank drive (1) should only move the carriage (2) but not the whole sub-assembly (Schneide_Schwenkteil) as it currently does...
Can you make the document public and share the URL?
IR for AS/NZS 1100
I hesitate making it public as it is IP of our company.
Please let me know how i can exclusively share it with you.
IR for AS/NZS 1100
I'll pm you my email you can share with.
He only wants to move the pivot arm (shown at 45°) for tool change over
and the purple linkage arm is a separate and continuous animation during machine operation.
because the rotation of the pivot arm changes the XYZ location of the purple arm. The rotation value of the purple also needed to increase by 90° while the pivot arm made it's motion.
because he only needs one at a time, we just made a couple of temporary locking mates to keep things in check.
he will just need to toggle between them depending on which he wants to move.
(would be easier if there were an assembly configuration checkbox... ahem
I'm also using the mate reset a lot to return to a default position.
I use your "lock" mates to define the positions, then suppress them and toggle around using positions. For the equipment to behave, it has to indeterminate which is your problem. What should move when I drag something? I think positions help here. I keep the "locks" as positions tend to need to be updated periodically. It's not that hard to maintain positions.
I use named positions a lot for this type of stuff.
I'm hoping for animations between named positions so I can get a piece of equipment to perform for me.