Welcome to the Onshape forum! Ask questions and join in the discussions about everything Onshape.
First time visiting? Here are some places to start:- Looking for a certain topic? Check out the categories filter or use Search (upper right).
- Need support? Ask a question to our Community Support category.
- Please submit support tickets for bugs but you can request improvements in the Product Feedback category.
- Be respectful, on topic and if you see a problem, Flag it.
If you would like to contact our Community Manager personally, feel free to send a private message or an email.
In Context? Derived? Configurations? Not sure which direction to proceed.

in Drawings
Another difficult time explaining in 'Onshapese' what I'm looking to do. The intent is to have maybe 6 parts based off of a single part and have those other parts be modified as or if the original part changes. Not sure which feature(s) to use to serve the intent.
Thank you
https://cad.onshape.com/documents/c7ac382255c4440e75bf4ef3/w/1f3e5ec88beba41434f1492d/e/4acce76f9471456354ecfedd
http://www.youtube.com/watch?v=9QQAxgw8SC4
Thank you
https://cad.onshape.com/documents/c7ac382255c4440e75bf4ef3/w/1f3e5ec88beba41434f1492d/e/4acce76f9471456354ecfedd
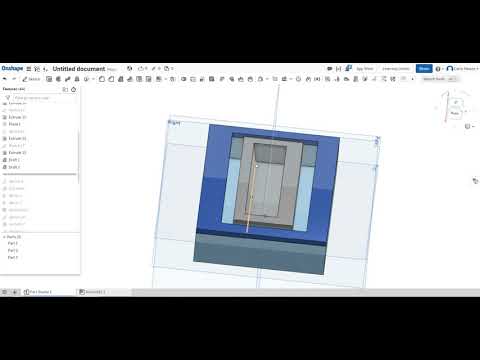
0
Best Answer
-
konstantin_shiriazdanov Member Posts: 1,221 ✭✭✭✭✭
from what you said configurations are well suiting such purposes
5
Answers
I also agree with @konstantin_shiriazdanov Configurations are the way to go in this case.
I hope this doesn't end up being 2LDR...
Here is a brief run down on each of the contextual types.
* In-Context: Used when you have a part with features that are based on an assembly's current position.
* Derive - Used when you have a part with features that are based on another part that exists in a separate partstudio
* Configurations - Used when you have a common part (or assembly), with slight variations
In general:
you should always use the path of least resistance (What is likely to change, what will always be the same). NONE of these contextual features are REQUIRED. You can do everything without them.
They are power tools that have just as many faults (when used wrong) as they do benefits.
They are there to save time / effort / mistakes on large projects by consolidating user input into fewer places.
You should never let there presence be a brick wall. If you don't understand them and use them wrong you will end up costing more time in the end.
Not to scare you off of them, they are extremely powerful when used right.
Difficulty/Maintainability:
In-Context is the hardest to maintain, as you must be responsible enough to verify your assembly is in the correct position, parts you don't need are hidden, Before you update the context(s).
In-context is here for a specific reason, you have a part that needs certain features to reference an assembly in one or more positions.
Derive also comes with great responsibility. It can be used as a tool to speed up a document, but when used wrong it can drastically slow down a document. Derive is said to be one of the slowest features on a tree (other than helix). The reason is it must solve the derived partstudio completely, then it will ignore the parts/sketches that you did not select. So if you want something to get wider when another part in another studio does, but that other part studio has 200 features on the tree. Then you're width relation in this studio costs as much as that other studio and this feature combined. There are ways to use derive to your performance advantage but I won't get into that here.
Unless you really understand the pros and cons (we can help you there too if you want) It is best to avoid them unless you need to reference an entire part in another part studio.
Configurations should be used sparingly as well, as they can add unnecessary complexity too (this is doubly true in sheet-metal). Only use them if you would otherwise duplicate a part studio or assembly, and only make a few minor changes, such as making a part that is generally the same but may be mirrored or wider etc.
Example:
You can by all rights draw a car tire from scratch, all of the tread, all of the lips and thickness changes. Then copy(duplicate) that studio then only change the inside diameter. A very quick model of a new part. Seems good right?
Now a customer comes in and wants a different tread pattern. Now you have to model that pattern twice, once for each part studio, but whoops! you made a typo when you made the change on the second tire size, and didn't notice until it was in full production, now you have a lot of defective tires that get recalled and all your tooling and machines need to be halted and re-manufactured.
If you were to configure the diameter in just one studio, that change would have reduced time/effort/mistakes.
In Conclusion:
These tools are just that, tools. Just because you have a power drill with 3 speeds and a hammer function, does not mean you should put a nail in the chuck use it as a hammer.
They all fill a specific niche. Each one can do basically the same thing in the end; just a different way of getting there. It is up to the modeler to decide which makes the most sense (if any) for this specific feature. I would say, if it is a confusing topic, then avoid using it until you have tested it in smaller projects or you have done your due diligence and learned as much as you can about their benefits and downfalls. There are many ways to model the same part. None are wrong if the resulting part is correct.
This wasn't meant to be this long, but I bolded the key points.
Need to experiment a little more and discover possibilities.
Thank you again!
Twitter: @onshapetricks & @babart1977