Welcome to the Onshape forum! Ask questions and join in the discussions about everything Onshape.
First time visiting? Here are some places to start:- Looking for a certain topic? Check out the categories filter or use Search (upper right).
- Need support? Ask a question to our Community Support category.
- Please submit support tickets for bugs but you can request improvements in the Product Feedback category.
- Be respectful, on topic and if you see a problem, Flag it.
If you would like to contact our Community Manager personally, feel free to send a private message or an email.
split surface of a body; add the option to keep face for remove face "leave it open"
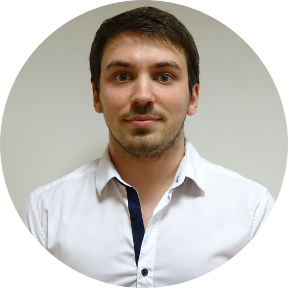
as what i was looking is to separate a face of a body (and keep the other surfaces), i would love to have this feature added maybe to the remove face, as it needs to create a copy before removing the original one, for the moment i am doing exactly this , i copy the faces i want to separate surface and after this i delete thel from the body obtaining the other surfaces (i am looking for this for easier boundary conditions for CFD).
the issue with this is that when copying surfaces, with offset surface (0mm offset) if the two surfaces are touching, then onshape will fuse the two faces.
the issue with this is that when copying surfaces, with offset surface (0mm offset) if the two surfaces are touching, then onshape will fuse the two faces.
Tagged:
2
Comments
i it is a simplified example, here i created a body ( a quarter of cylinder) and after that i used offset face at 0cm (3 times) to have the original body, and 4 extra surfaces (the top and down of the quarter can be in the same feature, and other two for each plane face) and after that, I delete the same faces in the body (with deleate face, with the leave open option).
my result is the same body that i am 100% that is watertight and separate in all the faces, I am doing this at least for the moment, as when importing the STL file for the CFD modeling I am having issues to separate the boundaries (normally they use min/max angle detection between faces) but for more complex geometries it is not working propertly (I insist i am learning so, maybe there are other ways to do this...)
thanks a lot for the quick answer!
I bet this could be done with featurescript
I am working with OpenFOAM, it is a CFD free software, and creating my models in Onshape to use for the simulations.
when I was working with Star CCM+ (another CFD software but in this case a commercial one) it was easy to set the boundaries of the simulations, the workflow was quite easy as I exported the model in.STEP format and in star CCM+ I could set the boundaries easily by selecting the faces I wanted (the inlet, outlet of the model, etc).
when I begin working with openFOAM I found that this is not possible to do it directly. OF works only with .stl models, so there are three main workflows to do:
- use one stl file (that contains all the surfaces) this is going to be watertight, and then separate the faces by feature angle, sadly this is not appliable to my models as it would create too many extra boundaries that in reality are the same one.
- use post-processing tools to detect the faces by eliminating other parts of the model (this is what I am using for the moment) this use one stl model only
- divide the stl file in different files with each one having the faces for each corresponding boundary. (what I was trying to achieve with onshape at this moment) . The issue is that when we export the "divided" surfaces, they do not share anymore the same points in the edges of the mesh, so after we reconstruct the same model it risk that it is not watertight anymore (even if before the exportation I would select the same faces in onshape and use enclosure feature and verify that it is watertight). obviously this method would be easier and more reliable as i could see everything from the onshape environment. what i found after a research in the subject is that in the software that this is possible to do, there is the option of meshing the solid in the same software before exportation (that is why i think it is a little bit too much "outside" of the onshape tools) for example, in blender or salome this could be done, where you take the solid, you mesh it, and after meshing it you export the model in a "exploted" files. I am sorry about bothering you guys as i think is a little bit too much out of the scoop of onshape to be done. but i was looking to be able to do it before i learned half of the things i have just point (sorry).
for the moment the solution i found is to export the model in a STEP model and do this process in salome.best regards, franco.