Welcome to the Onshape forum! Ask questions and join in the discussions about everything Onshape.
First time visiting? Here are some places to start:- Looking for a certain topic? Check out the categories filter or use Search (upper right).
- Need support? Ask a question to our Community Support category.
- Please submit support tickets for bugs but you can request improvements in the Product Feedback category.
- Be respectful, on topic and if you see a problem, Flag it.
If you would like to contact our Community Manager personally, feel free to send a private message or an email.
Extrude From (Starting Position)
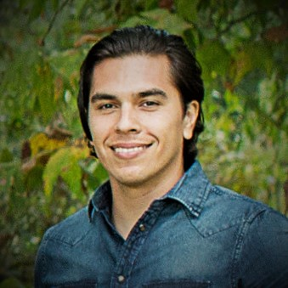
in General
According to the closing of this IR, there is no need for the "Extrude From" or starting position in Onshape, but I have a scenario that I think proves different.
Closed IR:
https://forum.onshape.com/discussion/comment/35060#Comment_35060


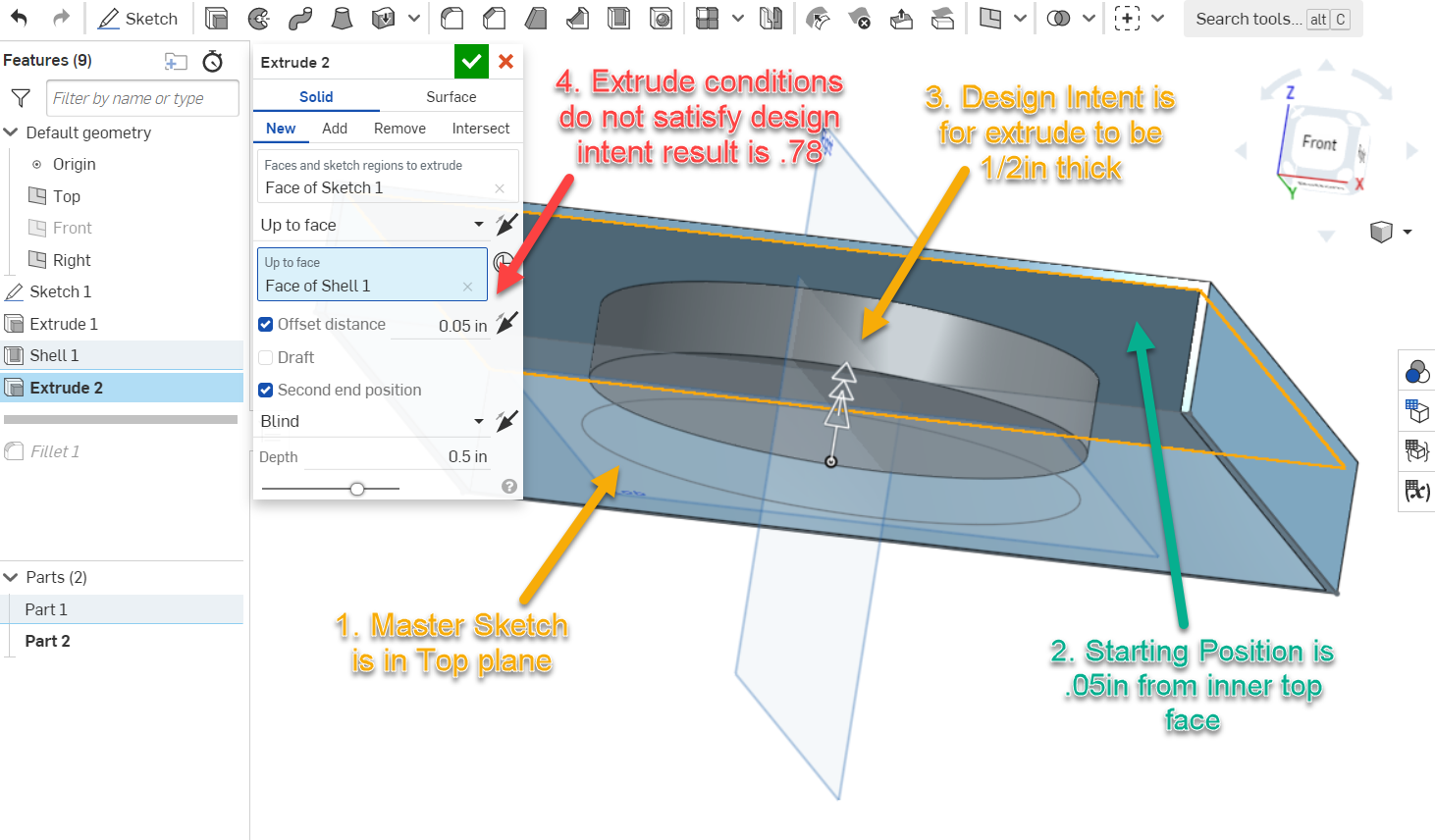
Closed IR:
https://forum.onshape.com/discussion/comment/35060#Comment_35060
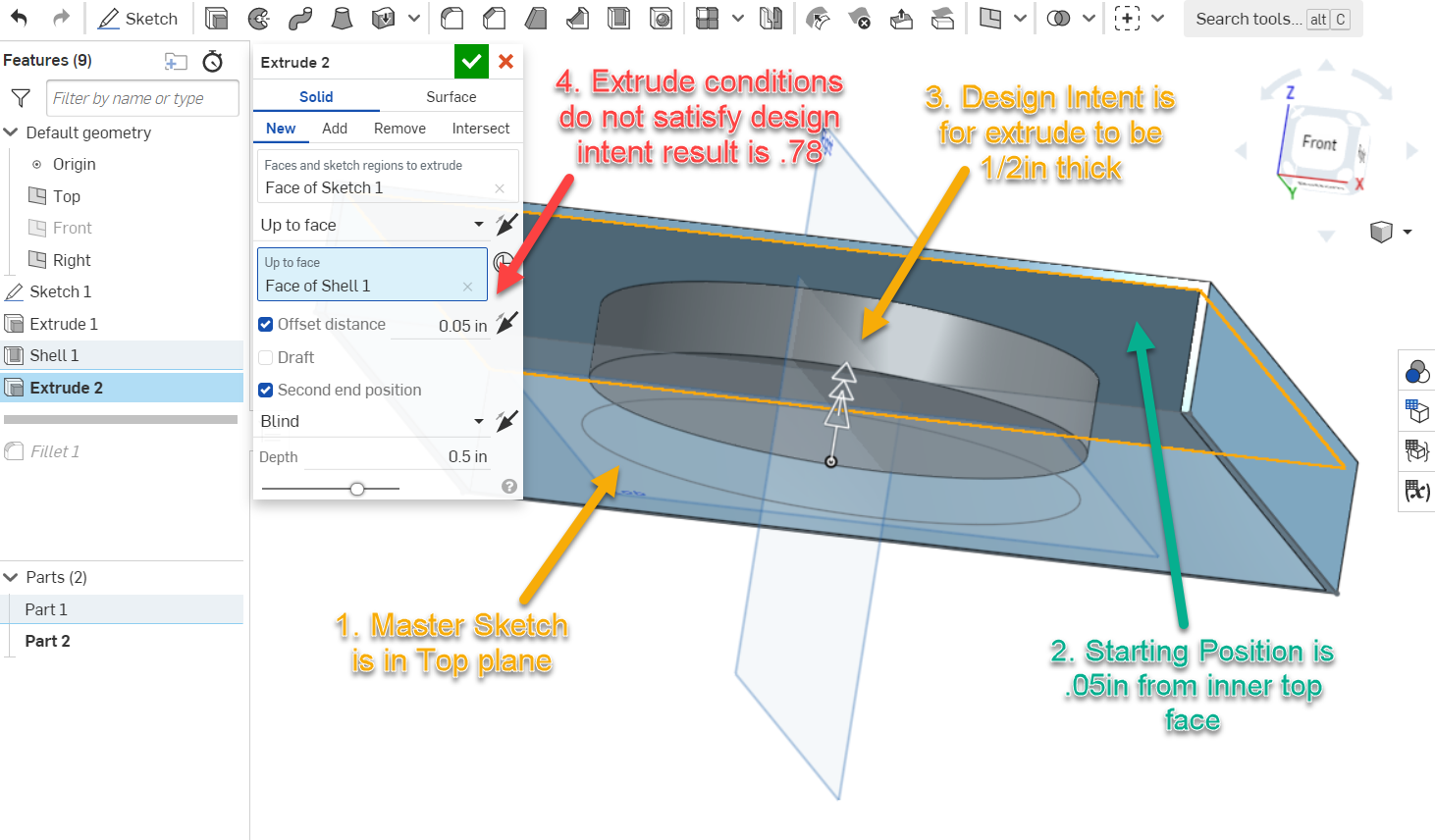
Adrian V. | Onshape Ambassador
CAD Engineering Manager
CAD Engineering Manager
Tagged:
4
Comments
CAD Engineering Manager
The Onsherpa | Reach peak Onshape productivity
www.theonsherpa.com
It's best to drag the handles into approximate locations:
Then attach to geometry:
This is the preferred way to do it.
Please leave solidworks behind and learn onshape.
And we are trying to leave SWx that's why we are asking for this missing use case.
CAD Engineering Manager
However, the current system doesn't let me model in draft the way that I've been doing it in Solidworks. I use a ton of extrude from vertex with draft. The draft hinges from the plane which is parallel to the sketch plane that contains the vertex. In Onshape the draft hinges from the sketch plane regardless of the other settings. I like to sketch a lot on the default planes and only create other planes when I absolutely have to (lofts etc). The Onshape way forces me to create extra planes or mate connectors and/or draft features.
Other things missing (compared with Solidworks):
Simon Gatrall | Staff Mechanical Engineer | Carbon, Inc.
I had a lot of issues with this feature in the beginning and Lou Gallo said that it had a lot of attention from focus groups to develop. He asked me to give it a chance. After about a month of playing with it, it started to sink in.
Maybe this could help, have both "up to face" reference the same face and then offset the furthest giving you the distance offset you're wanting, you don't have to compute it.
One thing to remember is the 1st end position has to be further away from the sketch than the 2nd end position.
Keep pushing them & good luck! If you need some help, let me know.
Using Ruled Surface accomplishes a lot of what one might want to do with an extruded and drafted surface. It's a decent work around. However, there are no options for extrusion depth or up to a surface or body (let alone offsets from these). The distance parameter of a ruled surface is not the same as the depth parameter of an extrusion.
Simon Gatrall | Staff Mechanical Engineer | Carbon, Inc.
I haven't played with ruled surfaces yet and want to. It was a missing puzzle piece and I'm glad it was added.
Since this thread is turning into a surface want list, how about extrude curve in this direction, and, let's add draft to that.
I'm not sure we'll ever stop wanting things, OS surfacing is pretty good these days.
Simon Gatrall | Staff Mechanical Engineer | Carbon, Inc.
CAD Engineering Manager
If I ever dipped my toe into Featurescript, the first thing I'd probably write is a stripped-down Extrude with nothing but inputs for the sketch regions and the two vertices. That would save me lots of mouse clicks!
Simon Gatrall | Staff Mechanical Engineer | Carbon, Inc.
Simon Gatrall | Staff Mechanical Engineer | Carbon, Inc.
I want a 10mm hole at a location specified face of rev1:
10mm entered and 10mm shown:
Here's a simple example of ruled surfaces:
* I have a non-planar parting line where the part needs to be split for 2 mold halves
* 7 features and 1 cleanup feature
* it's extremely robust and creates a well formed manifold
Then someone comes along and wants to make a changes:
* they change the size, curvatures & thickness
* can your model handle changes?
The simple anatomy using ruled surfaces:
* it starts with a surface shape containing compound curvatures
* then you create ruled surfaces for the top & bottom
* then you fill the top & bottom
* then I added a loft to form cleaner outer curvature
Surfaces used to create manifold:
* this manifold contains no slivers, shortened edges and gives you a clean part that can be used for downstream manufacturing
* some surfaces are just scaffolding for other surfaces which is typical for surface modeling, you build surfaces to create surfaces
* you can control complex shapes and capture design intent that'll speed development due to a clean b-rep manifold
The most important step:
This model is driven from a compound curvature surface and in this model it's declared as a datum stating that it's driving everything in this model. Datums don't have to be flat planes in parametric solid models. I think I'm mixing up forum threads, sorry, datums are important.
Having worked on 100's of injection modeled designs, this complex datum is always missing. To recreate it from trimmed faces is almost impossible and you never know if you have it right. All translations can give you solids and surfaces. Please include this datum in your dataset for the next guy.
Also, if you're creating injection molded parts, use surfaces. Even if it's for datum definitions only, your models will be clearer and better formed. Pushing geometry to their extremes in a solid model only creates sliver surfaces and issues making the geometry un-usable for subsequent manufacturing operations.
Have @Evan_Reese write you a feature script that does exactly what you need. That's what feature script does and as good as Evan is, he could write it less time than we've spent creating this post.
The Onsherpa | Reach peak Onshape productivity
www.theonsherpa.com
You can find plate extrude and my other plate suite features here:
https://cad.onshape.com/documents/2c2b49357f3f1a232881256a/w/6258e1943ecedc8606542dd7/e/78e9b9148efe7163309beca0
FRC Design Mentor - Team 1306 BadgerBots
Anyone know if there was an IR added, or this is being considered for inclusion??
There's still no direct way to "offset from face", specifying a distance. The only way I was able to create the desired scenario was to create a Mate Connector within the extrude feature. The issues with this is that the parameters for that mate connector are hidden within the Start offset Entity.
Yes the end-result is achievable, but my original request was not about end-result, was about the steps required to do so, and intuitive would be communicate design intent.
CAD Engineering Manager