Welcome to the Onshape forum! Ask questions and join in the discussions about everything Onshape.
First time visiting? Here are some places to start:- Looking for a certain topic? Check out the categories filter or use Search (upper right).
- Need support? Ask a question to our Community Support category.
- Please submit support tickets for bugs but you can request improvements in the Product Feedback category.
- Be respectful, on topic and if you see a problem, Flag it.
If you would like to contact our Community Manager personally, feel free to send a private message or an email.
Mates and assembly solving
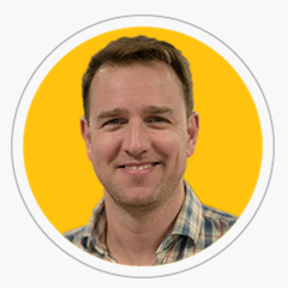
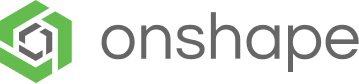
We want to make the process of mating parts in assemblies in Onshape as simple and efficient as possible. That led us to implement the mate connectors in assemblies and give you the ability to change mate types very easily.
I'd like to get your feedback on mate solving when adding new mates: After you have selected two mate connectors for a mate we move the parts so their relative positions are solved, but we don't solve the whole assembly until you click 'OK' or the 'Solve' button.
How do you feel about this partial solve of assembly mates?
In your experience does this help you get your parts mated faster and more reliably?
I'd like to get your feedback on mate solving when adding new mates: After you have selected two mate connectors for a mate we move the parts so their relative positions are solved, but we don't solve the whole assembly until you click 'OK' or the 'Solve' button.
How do you feel about this partial solve of assembly mates?
In your experience does this help you get your parts mated faster and more reliably?
Andy Morris / Head of Product Design / Onshape, Inc.
Tagged:
0
Comments
I like the partial solve because it satisfies the "non-committal" side of my brain, but it could be a bit better. If part 1 and part 2 are being mated, and part 2 already belongs to a mated assembly, OS consistently moves part 2 during the partial solve. I would rather have OS move part 1 (which is typically floating out in space), so the partial solve would be a bit more like a final preview.
It is more reliable for sure, as the mate connector concept is new, and I find myself toggling between revolute/cylinder a lot as I am trying to get the proper DOF's. The partial solve allows for that, and it is nice. The "animate DOF's" is an EXCELLENT feature. Really helpful!
Like I've mentioned before, this mate connector concept is on it's way to becoming one of the most innovative new CAD things I've seen in a long time. Well, you know, except for the whole "cloud" thing of course.
Linked[in]
I find i position a part, then want to offset it, only way to do this is with the mate connector. I would then right click on the part, switch to part studio, click on the connector to find it in the tree, then right click edit to bring up dialogue, then click on the move and type the offset. Long winded to get a simple offset.
Happy to use the connector for the offset just need better access to edit it. Initially was frustrated there was no offset mate but think I am over that now.
Twitter: @onshapetricks & @babart1977
Twitter: @onshapetricks & @babart1977
I've gotten bitten by this as well. I while ago I filed a feature request for them to not start a new action (create feature/insert mate/etc) until the current dialog has been either ok'd or canceled. I don't remember the outcome.
SW has mate connectors. (Called mate references.... ). They autosnap and work great for screws and other parts with repetitive ways of mating. (In a solidworks part you can add them with Insert->Reference Geometry->Mate Reference. Try them out next time you are in SW!)
Twitter: @onshapetricks & @babart1977
Positioning sub-assemblies requires a mate connector if you want to control it's position with offsets. Therefore add to the DOF the number of sub-assy's and you'll have the total mate connector count.
total mate connectors= assy DOF + sub assy's
I really think what is gone is the mate hell that we all experienced in past parametric systems. A top level assembly shouldn't have more than 20 - 30 mate connectors which is totally manageable. I think building OS assy's using old parametric techniques is a wrong idea.
Only problem I have is there is no way to replace a bolt and pick up existing mate, however mate is that quick to do you don't need to worry too much.
Twitter: @onshapetricks & @babart1977
I'm positioning components, deleting the mate, then adding to a group. The bolt stack up should probably be grouped with the part it's fastening. At the end of the day, you'll have very few mate connectors.
My assembly is going really well, it's clean, very easy to understand. I think it's the way forward. Much better than anything I've seen in the past.
Having transformations between each component is crazy, who ever came up with such a wild idea?
In SW's I do built dummy sub assy's, drop in and explode to save mating time. But this is better.
Twitter: @onshapetricks & @babart1977
I'm really trying to reduce mate count and come up with a strategy that minimizes the confusion. Mates in SW are crazy and difficult to follow.
You're example, 4 bar linkage, I think I could do with 6 mate connectors and have the same motion you have using ~25 mates. Most assemblies motions are simpler than your example and really take advantage of grouping.
Your dummy SW assy is similar to the group idea if you fixed all components in that dummy assy. I've never seen this strategy used in SW. The grouping workflow in OS is painless and easy to manage. Not sure how your dummy SW assy stacks up to OS grouping, I'll have to give that some thought.
Normally I would try to build parts up with complete set of fasteners attached in the top assy, this is useful for getting clearances/sizing, makes the assembly look visually finished off and needed to build the BOM on the drawings/parts manual's. Normally it time consuming and annoying in SW's I would quite often just do a concentric and face to face mate under the bolt head but you still have a loose parts have to come back later and lock down with a plane to plane parallel mate. I think some of these mating methods are much quicker and more robust.
Twitter: @onshapetricks & @babart1977
That's my design intent, which is different than yours. I'm on a mission to omit all mates except the ones that really matter.
FYI-grouping mated items throws an error with the mate connectors. As well, fixing mated items throws an error. In SW fixing items doesn't throw an error with mated items (I submitted that one and they fixed it). I submitted an OS fix-it ticket to stop throwing mate errors for fixed items. I'm wondering if grouped items should also be excluded from mate errors. I think so. Mates should error with other mates and not fixing or grouping.
You can't nest groups (add a group to another group). Only components can be added to groups. Not sure if this is a bug.
I still can't design in an assembly and have to dance around sub-assemblies & part studios. All this makes my head spin. I find having multiple OS sessions open in the browser is faster than dancing between document tabs.
You can't merge 2 part studios which really makes working with downloaded geometry a real pain. I'm trying to consolidate tabs but can't.
Suppose this is a reason. Hopefully fixed soon.
Twitter: @onshapetricks & @babart1977
Because you can't merge a downloaded bolt into a part studio.
Suppose this is a reason. Hopefully fixed soon.
Yeap it's turning out to be a real issue.
Moving components in a part studio requires a transform which can only handle translations or rotations. Typically you need 2 since you can't mix rotations & translations. You have to know the distances & angles. SW allowed constraints when moving bodies inside a part file, not so in OS. Also OS remembers everything so your tree has all these transformations locked up in perpetuity. I was hoping for a delete transform but leave geometry option. Positioning bodies in a part studio is a real drag.
Or, on second thought, why not have an option in the transformation dialog that logs the transaction to the feature tree or doesn't, maybe a "position only" option. I think most people won't want to log transformations into the feature tree.
Twitter: @onshapetricks & @babart1977
-I think everyone agrees the part studio trees are un-manageable.
-Put a part studio in an assy and it's tree is f'd-up.
-Go up one more level and now we have something manageable.
Bruce, I really think I could have done a better job at putting this together.
Do you have a strategy for large assembly management?
Sounds like your on the right track with reducing mates and keeping things clean. Hopefully this will make it easier when coming back into a model to work out how it was created, less maintenance and problems. Although I am expecting Onshape to come up with good methods/features to manage mates rather than the user getting rid of them altogether because they are unmanageable.
Twitter: @onshapetricks & @babart1977