Welcome to the Onshape forum! Ask questions and join in the discussions about everything Onshape.
First time visiting? Here are some places to start:- Looking for a certain topic? Check out the categories filter or use Search (upper right).
- Need support? Ask a question to our Community Support category.
- Please submit support tickets for bugs but you can request improvements in the Product Feedback category.
- Be respectful, on topic and if you see a problem, Flag it.
If you would like to contact our Community Manager personally, feel free to send a private message or an email.
Assembly Mate Stability: Hierarchy of Geometry
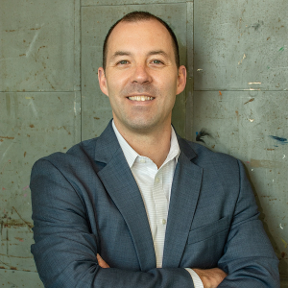
Quick question for the OS folks: In regards to Assembly Mate Stability, is there a hierarchy of geometry in OS?
Generally speaking, there is a "pecking order" up the food chain of geometry: Point/Vertex, Line/Edge, Surface/Face, Volume/Body.
For example, in ProE/Creo (Granite Kernel), it is generally regarded that creating assembly references to Vertices and Edges is a big no-no, since those references are blown away/replaced at will when sketches/features are edited and updated. Parasolid-based modelers (NX, SW, OS) are a bit more forgiving, and as such I have seen many edge/vertex referenced used with much stability (questionable design intent, however).
Things are a bit different with the Mate Connector concept, though...
Imagine I want to bottom out a bolt into a blind tapped hole in OS. When I choose the Fasten mate, does it matter if I reference the circular edge or the circular face? Is one more stable than the other? What if the surface is a "D" shape - should I reference the arc edge or the surface itself?
Thanks!
Generally speaking, there is a "pecking order" up the food chain of geometry: Point/Vertex, Line/Edge, Surface/Face, Volume/Body.
For example, in ProE/Creo (Granite Kernel), it is generally regarded that creating assembly references to Vertices and Edges is a big no-no, since those references are blown away/replaced at will when sketches/features are edited and updated. Parasolid-based modelers (NX, SW, OS) are a bit more forgiving, and as such I have seen many edge/vertex referenced used with much stability (questionable design intent, however).
Things are a bit different with the Mate Connector concept, though...
Imagine I want to bottom out a bolt into a blind tapped hole in OS. When I choose the Fasten mate, does it matter if I reference the circular edge or the circular face? Is one more stable than the other? What if the surface is a "D" shape - should I reference the arc edge or the surface itself?
Thanks!
Tagged:
0
Comments
It's does a great job of navigating through Mate Point selection, but it has nothing to do with the way it is assembled in real life, and so design intent is completely thrown out the window. I honestly think this demo leads new users down the wrong path, and should be removed/replaced.
Linked[in]
Some of the content, like this video were created a few months ago.... And now they need updating..... (This is a problem with a rapidly developing product). So I am about to update this example. I would like to understand in more detail how you would assemble the vice example?
care to elaborate?
As far as referencing edges or faces... I don't think there is a single answer. Your question is related to selections in general. It applies to all aspects of the product.
BTW, Going from a circle cut to a D cut works regardless of whether you select the face or the edge. The mate connector finds the correct reference.. Nether is fundemtally "better" since its a case by case answer.
On the topic of parametric selections, I am a big proponent of adding a level of abstraction to a selection. So instead of selecting the edge. you select "edge intersection" between two features. Let the system is figure out what is actually being selected at the entity level. This is inherently more robust. We are a ways off from implementing something like this. I just figured I would see what people think?
Roger that on the edge vs. face topic. One thing I found out, is that with a C-clip for example, there is a subtle difference. When the flat face is selected, the center of that area is not exactly in the center of the part (because the opening in the clip moves the centroid over), so the inner curve of the C clip must be used to grab the mate point if the user wants the C-clip installed properly. It's not as obvious as you'd think, especially since C-clips are pretty small relative to the overall assemble size.
RE: Parametric Selections - I'm having a tough time wrapping my head around that concept. Do you have a practical example?
Thanks @LouGallo and @MalayKumar! I hear ya loud and clear. I am really beginning to see just how versatile AND robust the mate connectors are. It is a really, really hard combination to get right, and you guys are on your way to something really special with it.
Linked[in]
First, dependency robustness. Quick experiments show that it's no better than solidworks... Sketch geometry is the most stable, solid edges are ok and solid vertices are fragile. Mate connectors can be to sketch geometry which will probably be my preferred reference geometry as I found that any operation that replaces a solid face will cause the mate connector that depends on it to fail (even when the original face is still in the history and builds fine. For instance if you created a through-hole feature over the top of your blind tap as a secondary operation... ) if it is between the original feature and the mate connector.
Second, mates and design intent. I'm not sure yet that mate connectors as the are now will satisfy my needs. I like that they provide a level of indirection. But the indirection makes me have to think a little harder too. I'm waiting to see how Onshape deals with more complex mate relationships like tangency, offsets and ranges. I get the feeling sometimes that Onshape thinks mates are only for kinematic marketing demos. I don't know about the rest of you guys but I use the mate solver and interference detection to catch problems that would prevent assembly and to help other engineers understand what the design intent is. If a boss seats in a pocket, a face mate and a tangency mate 1: makes it obvious exactly where the parts should be fitting together, 2: can help me understand how the part interferes with the rest of the world as it moves around in the pocket. (In case you're wondering, simple parts and assemblies don't get this treatment, I'm not that pedantic.)
I know exactly what you are talking about in the second paragraph. To be perfectly honest, if I can't do a tolerance stack analysis in OS, I won't be able to take it seriously. I've always got manufacturing on my mind, but I know others look at CAD from a different angle.
Alas, I'm not going to dwell too much on the current state of affair because by the time I finish writing this, a new build will probably be pushed out with some killer new stuff in it. I was just hoping to get some insight on this mate connector concept...
Linked[in]