Welcome to the Onshape forum! Ask questions and join in the discussions about everything Onshape.
First time visiting? Here are some places to start:- Looking for a certain topic? Check out the categories filter or use Search (upper right).
- Need support? Ask a question to our Community Support category.
- Please submit support tickets for bugs but you can request improvements in the Product Feedback category.
- Be respectful, on topic and if you see a problem, Flag it.
If you would like to contact our Community Manager personally, feel free to send a private message or an email.
Mating best practice?
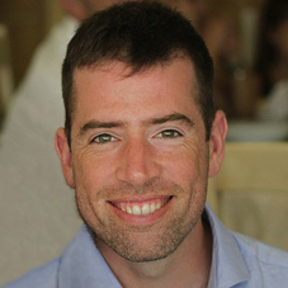
I feel like Onshape inverts the way I normally think of mates. A mate connector starts with 6 locked degrees of freedom (DoF) and I choose how many to unlock. In SW a mate gives me no locked DoF except for those defined by the mate.
Normally I try to match mates to how an assembly physically fits together with as few locked degrees of freedom as possibly so that the solver will make obvious things that cause assembly or stackup problems.
I'm slowly figuring out what mates to use for different situations but I'm curious what other people are doing.
Has anyone gotten to the point where they are using mates to really capture design intent and catch design problems?
Normally I try to match mates to how an assembly physically fits together with as few locked degrees of freedom as possibly so that the solver will make obvious things that cause assembly or stackup problems.
I'm slowly figuring out what mates to use for different situations but I'm curious what other people are doing.
Has anyone gotten to the point where they are using mates to really capture design intent and catch design problems?
Tagged:
0
Comments
I have not worked out how to do welded frames (rigid parts lock in position) yet, I have been doing them fully in the part studio then dropping in the assembly, grouping and fixing 1 part. Not ideal. I am using the part studio mirror and array but end up with multiple instances of the same part, this will not work with the BOM down the track. I am sure there is a work around but have not got it yet, kind of waiting to see how the drawings and document management(fastener library/sharing files between doc's) will work.
Twitter: @onshapetricks & @babart1977
I'm guessing that there will be patterns in assemblies to handle the first case and that the pattern feature is what one would use for the second case.
I have a mate connector in the receiving plate at the depth of the end of the screw, a fasten mate between that and the end of the screw, a planar mate between the held-plate and the screw head, and a revolute mate between the holes in the receiving and held plates.
This doesn't handle valid but non-concentric holes.
Like babart77, most my assemblies are static and don't move. I'm using the fixed mate connector a lot. I guess my reasoning for using an assy is to manage the feature list. Breaking up small assemblies into various parts helps keep my feature list shorter for each part studio.
I'm finding it painful having to scroll up & down the feature list. Breaking the design into many part studios seems to help manage this but I do lose association between features which sucks.
I'm still not sure I've perfected the part studio/assembly logic. I do know that the feature list are too lengthy and that I like putting mate connectors in part studios only to bind them together in an assembly. I'm not crazy about this approach and waiting to see someone come up with a great approach.
(The screws example is a bit contrived. In practice, if the screw is not the right length, you just pull another one out of the cabinet. However not all peg-in-hole fasteners are so easy to change.)
The part-studio/assembly logic happens to match my solidworks workflow (where I use a layout assembly to create interdependent parts, and a as-built assembly to capture construction). I have faith that the feature tree will get cleaned up to be more efficient to navigate before too long.
Twitter: @onshapetricks & @babart1977
So you would place a mate connector on the end of the bolt and offset mate connector at the bottom of the hole. Bolt should not change but if the plate thickness changes you see and error?
I have also though about minimum thread lengths and placing MC's on the start of the thread, but have decided the group the thread features at the start of the part studio so when suppressed it will blow through to all parts, checking thread length can be done with the section tool, looks really cool when the interfering threads stand out in red.
I finding i use roll forward and rollback a lot in the part studio, this seem to be the only way to order the multi part list. I agree tree management needs improvement and sure that is high on the list. I have started naming features which i would rare do in SW, I also found I have to leave the feature name in place so I know what type of feature it is.
Look forward to planes, patterns, arrays and mirrors in the assembly mode this will limit work in building assemblies
Twitter: @onshapetricks & @babart1977