Welcome to the Onshape forum! Ask questions and join in the discussions about everything Onshape.
First time visiting? Here are some places to start:- Looking for a certain topic? Check out the categories filter or use Search (upper right).
- Need support? Ask a question to our Community Support category.
- Please submit support tickets for bugs but you can request improvements in the Product Feedback category.
- Be respectful, on topic and if you see a problem, Flag it.
If you would like to contact our Community Manager personally, feel free to send a private message or an email.
Moving Energy Chain / Cable Track
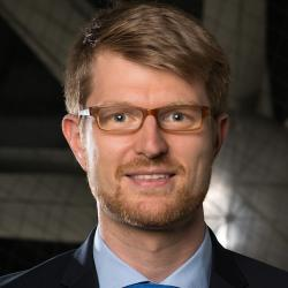
Hi!
I was just trying to get my head around how to create a moving energy chain in Onshape. In its easiest form something like this:

The whole shape is very regular. Of course it could be done "easily" with rotary mate in the joints limited to the maximum angle. But that would be quite tedious. What are our current options?

I was just trying to get my head around how to create a moving energy chain in Onshape. In its easiest form something like this:

The whole shape is very regular. Of course it could be done "easily" with rotary mate in the joints limited to the maximum angle. But that would be quite tedious. What are our current options?
- Part Studio => Pattern along sketch line controlled by variables (so the total length stays the same.
- Same as 1 but in context? But it does not update the PS when you move the assembly. But it could be updated, right?
- Assembling everything in an Assembly (started this with the first few joints for testing)
- Something useful with feature script to auto pattern "along a line" in the assembly.

0
Best Answer
-
philip_thomas Member, Moderator, Onshape Employees, Developers Posts: 1,381
I have built cable carriers like this before and it does work. The trick is to build a dummy part (an obround) that the links are mated to - works very well. Of course, that was before Managed In-Context and the next time i have to build one, i will create a single part based on the assembly position (in context). If i need to update it at any time, i will simply update the context - the main benefit is the absence of computational overhead until i need to update it.Philip Thomas - Onshape5
Answers
In other programs I would create the parts and link then together in the assembly. In onshape I might try to create a sketch with points where the sections are and use replicate to auto populate the parts in a assembly.
If you want full movement I would import the part into the parts studio and add a mate connectors. Theb in the assemble use snap and rotation mate to joint the parts together.
@philip_thomas that is a good way. With being able to recall versions an put different versions into drawings this is easy enough for now.
@carl_von_ayres I like the two end positions style as well. However I have 12 end positions depending on the product for 1 chain length. That might get a bit messy.
https://cad.onshape.com/documents/d40f5136cf73e5f7c4501627/w/41bb89af34b99c46ea64870f/e/5e0be2eeb769ac672738e538
something like this @philip_thomas ?
you may want to mute the video...
Here are a couple of examples that might stir the creative juices.
The real time example is obviously fiddly to build and slow to solve (complexity).
The Managed In-Context example is simpler to build and faster to solve (just update the context whenever you need a solution)
https://cad.onshape.com/documents/7aef7a09827d003f884c3cca/w/99c06602423584341085b649/e/3b3e94909e98c793235d7526
https://cad.onshape.com/documents/eb014ae849908dd1567b654c/w/ac8e8094f75706347ddea16d/e/ea97c3a384c30531e46e0a8e
Nice work Mr. Cooke.
Did you 3D model the rivets or is that a sneaky look at a new SM feature?
Owen S.
HWM-Water Ltd
HWM-Water Ltd
Owen S.
HWM-Water Ltd
In the echain assy, I had to replace the Fix of the Start Link with a fasten mate to keep it positioned properly relative to the slider mate when you insert this into the upper level assembly (Fix goes away at upper level).
I fixed the actuator base and the start link in the upper level.
I then created a 2:1 linear relation between the echain slider mate and the actuator slider mate.
After that, it works well (no noticeable performance difference compared to echain alone).
https://cad.onshape.com/documents/7cc175f8d6e311a7ff97a6fc/w/dee11f53c0929ee1920b606f/e/fa8d8be65e7c31be650cff4b
That IS nice work.
Would you mind allowing us to Copy your document (it's currently set to View Only without permission to copy)?
It's a very helpful assembly to be able to use in our equipment development too.