Welcome to the Onshape forum! Ask questions and join in the discussions about everything Onshape.
First time visiting? Here are some places to start:- Looking for a certain topic? Check out the categories filter or use Search (upper right).
- Need support? Ask a question to our Community Support category.
- Please submit support tickets for bugs but you can request improvements in the Product Feedback category.
- Be respectful, on topic and if you see a problem, Flag it.
If you would like to contact our Community Manager personally, feel free to send a private message or an email.
I need help with my Music Box
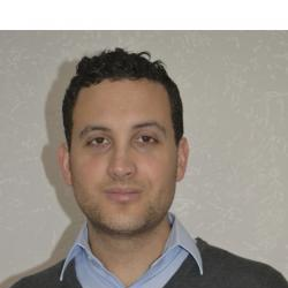
in General
Hi Onshape Forum,
I started to model a Music Box (Crank Box) and reached my limits. I am new to CAD and don't know how to realise the following:
1. How can I get pins on the cylinder (Doesn't need be accurate, just random pins across the cylinder)
2. Is there a way to add a plane in the middle of the cylinder in order to mirror the yellow part?(Pic. 2) I only managed to get a plane in the wrong direction.
3. I see in many Onshape sample files screws and screw wholes. Is it common to import screws from e.g. GrabCAD and make the wholes in Onshape or how is this normally done?
I have made the model (Musik Box) public now and hope you can help me to answer above questions.
Thank you and best regards,
Tarek
I started to model a Music Box (Crank Box) and reached my limits. I am new to CAD and don't know how to realise the following:
1. How can I get pins on the cylinder (Doesn't need be accurate, just random pins across the cylinder)
2. Is there a way to add a plane in the middle of the cylinder in order to mirror the yellow part?(Pic. 2) I only managed to get a plane in the wrong direction.
3. I see in many Onshape sample files screws and screw wholes. Is it common to import screws from e.g. GrabCAD and make the wholes in Onshape or how is this normally done?
I have made the model (Musik Box) public now and hope you can help me to answer above questions.
Thank you and best regards,
Tarek
0
Best Answers
-
jakeramsley Member, Moderator, Onshape Employees, Developers, csevp Posts: 665
For #2, hide the yellow part and in the plane dialog choose "Mid Plane". In the selection field, select the two end faces of the cylinder. This will make a plane that is between both faces.Jake RamsleyDirector of Quality Engineering & Release Manager onshape.com5 -
jakeramsley Member, Moderator, Onshape Employees, Developers, csevp Posts: 665
To make the pins, there are a couple different approaches to replicating them in the right location. Depends how accurate you want to make them. I'll try to show the first couple steps that I would use.
1. Start with a plane that is perpendicular to your cylinder and start a sketch on it. Select the two edges of the cylinder and use them (I then convert them construction).
2. Make a point that is the mid-point of one of the lines projected.
3. Use that point as a start for a linear pattern. I counted 20 different levels for pins (I'm probably bad at counting). Pattern this point 20 times and constrain the last one to be the mid point of the other line. Remember to delete the dimension first to allow the pattern to be defined by the midpoint. These points are where we define the different levels of the pins.
4. Make a plane at one of the points and use it to sketch on. I used a line point plane and selected the line from the linear pattern as the line and the point from the pattern.
5. Sketching on that plane, I'd make a construction circle that is the same size as your cylinder. I'd then make an offset of that circle that signifies the size of the pin. I'd then make construction lines from the center to the edge of the circle that represents where each pin would be. I dimensioned them relative to one another to get them constrained as well as knowing the angle between them.
6. Make a plane that is perpendicular to one of the points. I used a line point plane.
7. Sketch a circle on that plane that is coincident to the point. Dimension it to the size that you want.
8. Extrude that circle into the first cylinder you made and have the termination up to surface. Have it go up to the cylindrical face. I keep it as new so I can pattern the pin later and modify it.
9. From here, you have a couple options to replicate the pins. If they are evenly spaced around the cylinder you can use a circular pattern. If they aren't you can make individual copies using the rotation feature in transform. Use the angles used in your sketch to determine how much to rotate them.
Do this N number of times until you get the pins that you wanted. From here, boolean everything together.
Jake RamsleyDirector of Quality Engineering & Release Manager onshape.com5 -
3dcad Member, OS Professional, Mentor Posts: 2,476 PRO
1. Create circumscribed polygon in the place of rotating cylinder, set amount of sides to match amount of different angles you need for pins.
Note that the more you create sides the more work you will have but it will be more accurate.
Set dimension between opposite sides to be 'diameter of cylinder-x' (x can be anything, it's just for reference) I used here 90 for polygon and 100 for cylinder.
2. Extrude in same length as cylinder will be
3. Click on faces of polygon and create circles or whatever geometry the pins are.
Note that only the ones in middle line of side will be exactly tangential with the cylinder.
4. Extrude in length x+outcome of the pin, choose ADD for extrude.
5. Repeat creating the sketch + extrude for each side of polygon.
6. Sketch the final cylinder overlapping polygon and the pins leaving only the head visible, choose ADD for extrude
Note that I have used symmetric for extrude type, it's not necessary but I like to create everything in the middle.
7. Add fillet to all pin heads
//rami5 -
brucebartlett Member, OS Professional, Mentor, User Group Leader Posts: 2,146 PRO
@tarek_mustafa Love these little music boxes. I did a copy and started playing with this last night. I came up with a different method again, draw your lug on the top plane sketch referencing the finger and the cylinder. Extrude to the cylinder then move the top face to the right height, no new planes needed.
Then use a Circular Pattern with the face pattern checked, Face Move and Delete Face to position the lugs. I was thinking (music theory) 8bars then splitting into 4 beats per bar so rotate lug on multiples of 11.5 deg's you could use a simple equation in the move face angle eg 3rd beat of the first bar 11.5*3, 2nd beat of the 3rd bar 11.5*10. If a note is required more than once per rotation you need the pattern or draw another lug in and move face again, move face copy could be handy. If note not required use the delete face. Many ways to skin a cat.6 -
3dcad Member, OS Professional, Mentor Posts: 2,476 PRO
@tarek_mustafa
About screws, usually in mechanical design screw threads are not modeled (or are just for make it nicer view), details are marked in the manufacturing drawing. On the other hand 3d printers don't read drawings so for those everything needs to be modeled exactly as they are.
I'm not expert when it comes to threads but I know yo can create them using helix and proper sketch to sweep around. If I have understood correctly, creating new part from thread and groove using boolean subtract might give you better result.//rami5 -
_Ðave_ Member, Developers Posts: 712 ✭✭✭✭
@tarek_mustafa Typically the threads in the holes are never modeled. The common options are to model a pilot hole for the tap drill with or without a counter bore to represent the major dia. of the threads to depth. A hole wizard (hopefully coming soon) will do this for you. As for the screws it is very common to import a model from a vendor I use McMaster Carr for downloading hardware models they provide very well done models which are easy to locate and download. HTH
5
Answers
1. Start with a plane that is perpendicular to your cylinder and start a sketch on it. Select the two edges of the cylinder and use them (I then convert them construction).
2. Make a point that is the mid-point of one of the lines projected.
3. Use that point as a start for a linear pattern. I counted 20 different levels for pins (I'm probably bad at counting). Pattern this point 20 times and constrain the last one to be the mid point of the other line. Remember to delete the dimension first to allow the pattern to be defined by the midpoint. These points are where we define the different levels of the pins.
4. Make a plane at one of the points and use it to sketch on. I used a line point plane and selected the line from the linear pattern as the line and the point from the pattern.
5. Sketching on that plane, I'd make a construction circle that is the same size as your cylinder. I'd then make an offset of that circle that signifies the size of the pin. I'd then make construction lines from the center to the edge of the circle that represents where each pin would be. I dimensioned them relative to one another to get them constrained as well as knowing the angle between them.
6. Make a plane that is perpendicular to one of the points. I used a line point plane.
7. Sketch a circle on that plane that is coincident to the point. Dimension it to the size that you want.
8. Extrude that circle into the first cylinder you made and have the termination up to surface. Have it go up to the cylindrical face. I keep it as new so I can pattern the pin later and modify it.
9. From here, you have a couple options to replicate the pins. If they are evenly spaced around the cylinder you can use a circular pattern. If they aren't you can make individual copies using the rotation feature in transform. Use the angles used in your sketch to determine how much to rotate them.
Do this N number of times until you get the pins that you wanted. From here, boolean everything together.
1. Create circumscribed polygon in the place of rotating cylinder, set amount of sides to match amount of different angles you need for pins. Set dimension between opposite sides to be 'diameter of cylinder-x' (x can be anything, it's just for reference)
2. Extrude in same length as cylinder
3. Click on faces of polygon and create circles or whatever geometry the pins are.
4. Extrude in length x+outcome of the pin, choose ADD for extrude.
5. Copy sketch to other faces and adjust placement. Yes I know you would like this, it's not possible yet but you can send feedback and request for 'Copying geometry between sketches' to make it higher priority. So at the moment, repeat creating the sketch + extrude for each side of polygon.
6. Sketch the final cylinder overlapping polygon and the pins leaving only the head visible, choose ADD for extrude
7. Add fillet to all pins
8. You should end-up with only 1 part, if not just boolean all together.
@tarek_mustafa I will add some screenshots if you are interested in this approach?
This is probably the most time consuming part in your design and just to remind: you are not able to spin the cylinder and see the movement of 'fingers' when they touch the pins of the cylinder - they will just move through at the moment.
@JakeRamsley @LouGallo @AbeFeldman
I would love to see Ons pop those fingers when material is set to flexible, this would help to determine design problems in locks and other parts that temporarily bend/move to allow other parts movement 'through'.
Note that the more you create sides the more work you will have but it will be more accurate.
Set dimension between opposite sides to be 'diameter of cylinder-x' (x can be anything, it's just for reference) I used here 90 for polygon and 100 for cylinder.
2. Extrude in same length as cylinder will be
3. Click on faces of polygon and create circles or whatever geometry the pins are.
Note that only the ones in middle line of side will be exactly tangential with the cylinder.
4. Extrude in length x+outcome of the pin, choose ADD for extrude.
5. Repeat creating the sketch + extrude for each side of polygon.
6. Sketch the final cylinder overlapping polygon and the pins leaving only the head visible, choose ADD for extrude
Note that I have used symmetric for extrude type, it's not necessary but I like to create everything in the middle.
7. Add fillet to all pin heads
Then use a Circular Pattern with the face pattern checked, Face Move and Delete Face to position the lugs. I was thinking (music theory) 8bars then splitting into 4 beats per bar so rotate lug on multiples of 11.5 deg's you could use a simple equation in the move face angle eg 3rd beat of the first bar 11.5*3, 2nd beat of the 3rd bar 11.5*10. If a note is required more than once per rotation you need the pattern or draw another lug in and move face again, move face copy could be handy. If note not required use the delete face. Many ways to skin a cat.
Twitter: @onshapetricks & @babart1977
1. Draw and extrude a Polygon as described by #3dcat, I aligned it directly to the comb
3. Extrude all pins (use "new") and add a fillet. After that I used "circular pattern" to make 5 copies of the pin row
4. I used the "Transform" - Rotate tool to move various pins around. I did that three time for this model.
5. Last I made another Sketch with a cylinder (slightly bigger than the polygon) and extruded the same size as the polygon. Than I marked all and used Boolean.
I will continue now and try to finalise the Music Box. Thank you all again for your support.
Twitter: @onshapetricks & @babart1977
Maybe you can help me with another question regarding the screws. Is it common to import the right screws or to model as well? I would like to know how to make screw wholes that perfectly fit to one screw?
About screws, usually in mechanical design screw threads are not modeled (or are just for make it nicer view), details are marked in the manufacturing drawing. On the other hand 3d printers don't read drawings so for those everything needs to be modeled exactly as they are.
I'm not expert when it comes to threads but I know yo can create them using helix and proper sketch to sweep around. If I have understood correctly, creating new part from thread and groove using boolean subtract might give you better result.
Great skills, nice model! I wonder how long it will be before Onshape can predict the vibration frequency of a comb tine, by analysis of the inherent physics? Wouldn't it be cool to be able to turn the drum of the computer model and hear the real tune!
I agree with what the others say about how we normally approach the use of screw threads and whether they are modelled in detail or not.
The model attached is one I did recently just to test the possibility and accuracy of Onshape. There are two assembly tabs. The first one is the original; the second one I created when the screw constraint was added to Onshape recently.
Hope the example helps answer your questions as to how.
https://cad.onshape.com/documents/7bf6e574fc944b11b3cf6d5d/w/bce9145f8201438f99283a86/e/5741a1aa4dfe40f1ac2bff09
It is good to know that screw threads are usually not modelled, thanks for@
I agree with you @Andrew_Troup playing the sound in Onshape would be amazing, also to see the fingers pop when touching a finger as @3dcad mentioned perviously would be cool.
Thank you @R.Paul that is a great example.