Welcome to the Onshape forum! Ask questions and join in the discussions about everything Onshape.
First time visiting? Here are some places to start:- Looking for a certain topic? Check out the categories filter or use Search (upper right).
- Need support? Ask a question to our Community Support category.
- Please submit support tickets for bugs but you can request improvements in the Product Feedback category.
- Be respectful, on topic and if you see a problem, Flag it.
If you would like to contact our Community Manager personally, feel free to send a private message or an email.
How to use uploaded part in a Part Studio?
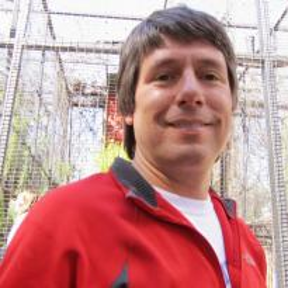
Hello,
I am probably missing something but I cannot figure how this.
I created a new document and in the Part Studio I started to create a plastic enclosure. Now, I have a PCA in solidworks and I exported it in Parasolid format. While in the Document I clicked Upload and I was able to upload and Translate the PCA and it showed up in an Assembly tab. I added the enclosure to the assembly.
What I would like to do, in the context of the assembly, is to use the mounting holes in the PCA to create the bosses in the enclosure. It does not seem like I can edit the enclosure in the assembly, and i can not find a way to insert the PCA assembly into the Part Studio where I can edit the enclosure.
Can someone please point out what I am missing here?
Thanks,
Christopher
I am probably missing something but I cannot figure how this.
I created a new document and in the Part Studio I started to create a plastic enclosure. Now, I have a PCA in solidworks and I exported it in Parasolid format. While in the Document I clicked Upload and I was able to upload and Translate the PCA and it showed up in an Assembly tab. I added the enclosure to the assembly.
What I would like to do, in the context of the assembly, is to use the mounting holes in the PCA to create the bosses in the enclosure. It does not seem like I can edit the enclosure in the assembly, and i can not find a way to insert the PCA assembly into the Part Studio where I can edit the enclosure.
Can someone please point out what I am missing here?
Thanks,
Christopher
Tagged:
0
Comments
You can also translate the assembly into a parasolid and then re-translate into a part studio but that's much help as you will lose your history tree for the part already started. Best to start with the parts you want to build around in a part studio and go from here.
Hope this helpful
Bruce
Twitter: @onshapetricks & @babart1977
Thanks for the help!
Christopher
Beware that Onshape is not friendly to collaboration with external tools. Import and export are one-time things. The tabs say "update" but what they mean is 'delete this and upload a new one'. So make sure you are happy with your SolidWorks model before bringing it in.
I like your answers a lot, but I'm not convinced you're in the right thread.
I could be wrong here, and sure we have to read between the lines somewhat, but isn't the OP essentially importing a parasolid assembly into Onshape, and wanting it to end up in a Part Studio so he can do stuff to it?
Yeah, I guess it does read a bit strangely. I went to answer the question and then saw that Bruce had done so, so I stripped out everything that was redundant which left the posts being tips for SW users rather than the OP's original question.
Really a nice update..
It seems from a cursory look that we don't get any discretion in the location of the derived item in the destination studio. Or do we?
(Not that it matters, in the casting/machining situation ... but in the case of, say, derived sketches, in particular, it seems to me that would frequently be essential. Maybe we can work around it in the short term by copying and pasting, but then we lose the live link....)
As I understand it, the item arrives in the same relativity to the datum planes as it had in the studio it came from, but I hope I have that wrong.
I though this could be used for all static standard parts which don't need moving mates. But using transform to place the parts is a no go.
Derived Sketches, even more so. Destination plane might be at a compound angle to the origin plane; transform would be a nightmare.
Derive could be insanely great, if this were addressed.
And derived sketches# need to be available within a Studio as well as between them.
# arguable true also for bodies: "Copy in place" might seem an acceptable workaround here, but once again the transform option is unappealing, in cases where we need to relocate the body to an absolute location, rather than relative to the previous location.
In designs which are heavily non-orthogonal but with repetitive elements (cockpit displays for a flight simulator?) I think there is an associated need for simple creation of named reference axes, able to be picked directly from the feature list.