Welcome to the Onshape forum! Ask questions and join in the discussions about everything Onshape.
First time visiting? Here are some places to start:- Looking for a certain topic? Check out the categories filter or use Search (upper right).
- Need support? Ask a question to our Community Support category.
- Please submit support tickets for bugs but you can request improvements in the Product Feedback category.
- Be respectful, on topic and if you see a problem, Flag it.
If you would like to contact our Community Manager personally, feel free to send a private message or an email.
BOM of vendor parts like ball bearings
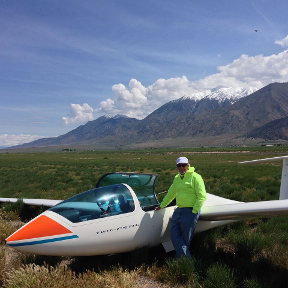
I don't know whether this is a question for OpenBOM or OnShape but here's my problem.
When I create a parts list BOM, every ball in the bearing is treated as a separate part. This is nonsense. A ball bearing is just one part no matter how many internal parts there are. How can I force OnShape and Open BOM to treat vendor parts with many internal components as single part?
I know how to group a bearing in order to move it around an assembly but when that assembly is incorporated into another one, the group is lost.
When I create a parts list BOM, every ball in the bearing is treated as a separate part. This is nonsense. A ball bearing is just one part no matter how many internal parts there are. How can I force OnShape and Open BOM to treat vendor parts with many internal components as single part?
I know how to group a bearing in order to move it around an assembly but when that assembly is incorporated into another one, the group is lost.
Tagged:
1
Best Answer
-
billy2 Member, OS Professional, Mentor, Developers, User Group Leader Posts: 2,100 PRO
bill_daniels thanks for posting this. We need good BOM's.
I'm finding that partstudios should be inserted into an assembly before inserting into a top level assy. I'm not here to justify this but find OS behaves better this way. Seems like an extra step, but works best if you do so.
There is an enhancement to make partstudios behave like sub-assemblies in OS and Tim Rice can add you to this list if you want. Sounds like adding your partstudio to an assembly will clean up your BOM. I'm hoping so.
Getting the top level assembly structure correct with all the sub-assemblies is no easy task. But, since OS is new and driven by a database, possibly we can get BOM's right this time or closer to correct.
Most solidworks people I know create the BOM in a spreadsheet and detach it from the CAD. Hope this changes since I don't have excel loaded on my computer.
5
Answers
There are a couple of options you can do to help:
1. Boolean all the components together so that it becomes a single part.
2. Put all the components into their own subassembly. Then you can put that subassembly into your main assembly. After that, choose a "Single Level BOM" for OpenBOM when creating the BOM.
For most things like bearings where you don't need the detail or need to simulate any motion of the components, the first option is usually the better one.
You will get better loading and rendering performance with the first option as well.
As always I will leave it to the expertise of @oleg_shilovitsky to correct me on anything.
Twitter: @bradleysauln
Thank you for asking! Unfortunately, there is no way to say in Onshape that multiple bodies in PS are actually a single part. This is a scenario we're discussing with Onshape and potential solution is to work some Part classification that can help us to do so.
There are few workarounds I can suggest.
1- The one proposed by @robert_morrisTo put all balls in a separate assembly and create "single level" BOM using openBoM.
2- Restructure BOM after creation using new "restructure" tool in openBoM Multi-level view. This is a new functionality and we still considering it very much experimental. However, we've got very positive feedback on it. Check the following video for more details -
3- Future option to define item classification parameter to treat specific parts in PS as a single part. It can work in combination with multi-level BOM. This option is current under research /development.
Please feel free to contact me directly if you have any questions oleg @ openbom dot com.
Best, Oleg
@bradley_sauln thanks for brining me to this discussion! I missed that yesterday.
For many reasons, I want the option to force a bearing or other vendor item to behave as the vendor intended. For example a bearing's inner and outer race should rotate with respect to each other as if they wear attached with a revolute mate. I've tried to do this but I can't seem to get it to work.
I'm finding that partstudios should be inserted into an assembly before inserting into a top level assy. I'm not here to justify this but find OS behaves better this way. Seems like an extra step, but works best if you do so.
There is an enhancement to make partstudios behave like sub-assemblies in OS and Tim Rice can add you to this list if you want. Sounds like adding your partstudio to an assembly will clean up your BOM. I'm hoping so.
Getting the top level assembly structure correct with all the sub-assemblies is no easy task. But, since OS is new and driven by a database, possibly we can get BOM's right this time or closer to correct.
Most solidworks people I know create the BOM in a spreadsheet and detach it from the CAD. Hope this changes since I don't have excel loaded on my computer.
1. It's one solid part so it behaves correctly.
2. It can be labeled as if it were really the bearing.so OpenBOM handles it correctly.
While reverse engineering the external shape of ball bearings is relatively easy, more complex parts like electric motors involve a lot work. The mass parameters are also completely wrong.
Another option we considering to add to openBoM / Onshape integration scenario is to mark specific parts "exclude" from BOM. We support such flag in openBoM / Solidworks integration and it helps to get rid of unnecessarily parts.
what do you think about that?
along the lines of simplifying your bearing, Why not draw an inner and outer diameter over the bearing and extrude to it's thickness? Then figure out some how to make that simplified representation show up and go away with suppress/un-suppress.
OS would appreciate reducing those spheres from a display perspective.
At any rate, the BOM should behave regardless of the display state. Also, I think weight should be entered by engineering as meta data. Making the geometry match real world could be time consuming, involves density and other hard things to consider.
There's much to figure out.
For instance:
-what are the raw stock sizes that needs to be purchased to machine a part
-I want instancing (there are 5 of these in my assy, I need 5
-this comes from common stock (nuts, bolts, washers)
-use this as required (loctite, glue)
-I want disc, part number, phone number, web site link, lead time and price
BOM's will only occur in an assy because partstudios don't have instancing. Getting the assembles right is the next thing in the evolution of a BOM. How will they solve this?
I met OpenBOM at MDM in Anaheim Ca. and these guys are serious players. I'm hoping they're focusing on the operations side of a project that's bi-directional with OS. Stockroom management, forecasting, and ordering. OpenBOM should allow real time pricing and part lead time for a project design. It should be a tool for the purchasing department to sync up with engineering.
Not sure where this division will occur, hoping OS supplies a real engineering BOM this time.
We are thinking alike about many topics you mentioned. Our first goal is help to get rid of spreadsheets for BOM. Then we will come with cost, online pricing, inventory, ordering and more.
Best, Oleg
For bearings, I always try to get them modelled as single parts with the properties added so they show up in my BOM's correctly, sometimes I will add a mate connector for easy mating on a centre line where the internal diameter is offset. For vendor parts with movement like Gas Struts, Hydraulic Rams, Linear Actuators, Etc I model with the movements set by mates but simplify the parts as much as possible into single part movement groups, I don't worry about the fine detail but try to keep weight in mind to get as close as possible, especially for heavy parts. For these assemblies I add properties to the assy and leave the subparts blank.
It got me thinking about the future and the quickest way to get my bearings or other vendor parts into my Onshape. What I really want to be able to do is just insert directly from Onshape through some kind of Vendor link up but with my meta data, I also want to easily to be able to change parts without messing with mates and have updates show up from vendors. I really think this is the future for Onshape, because at the moment with downloads, imports and clean up's lot of design time is wasted data management.
Twitter: @onshapetricks & @babart1977
Where are you now?
I totally agree with you.
I looked at the Thomas Enterprise app, didn't down load it either. Is David Bandi delusional? There's no way I'd install that program on my computer just to get a part file. With the new un-abated internet rules in the USA, installing a program on your computer is quick way for them to scan your hard drive, phone home and do what ever they want. David is dead wrong, missed the boat, walked off the dock, floating down river.
I was very supprised I had to download and install an app, can't believe a parts vendor would go with a system like this. My goal is to keep everything in the cloud no downloads or imports just straight in as native Onshape. For this to happen we have to have vendors loading their data, most vendors certainly see valve in making models available, they now just have to see valve in having it in Onshape. (Larger use base and customers requesting Onshape from vendors will help here). On the Onshape side I believe there still needs to be some development around a decent library system, configurable parts and assy's and a way to add your own meta properties to vendors models. Look for to some improvements here.
@bill_daniels I ended up using a SKF bearing.
Twitter: @onshapetricks & @babart1977
I would also like to connect BOM into ERP so that it is easy to sync part numbers and other data back and forth. But please do not say only way to do this is sending an xml. I don't know who is trying to fool who but xml is just dummy text file like csv. I would really like to see Onshape/openBom opening dataconnections to be used with SQL which doesn't involve any export/import procedures. Just show the data in different places from single source of truth.
ps. I tend to build assemblies using part studios and at later point I select them from main assy and move to new subassembly.
Checked weather in the Rockies for you,
I-70 could have snow on Tuesday
I-80 seems to have rain/snow on Tuesday
Check weather before you head East, the Rockies have altitude and the weather will change as you cross over the continental divide. FYI, I've been in Denver and it snowed in July.
Yeah, I don't know why anyone would write a desktop app to manage file down loads. It's the first time I've realized how dangerous the desktop space can be from a security perspective. Browser's use javascript which doesn't have access to a local hard drive except to upload. True cloud apps can't scan your hard drive. To gain access to your local hard drive, you have to have installed something. My recommendation is don't.
Suppliers really need to step up their game and so the does the industry in general. I still download supplier data that doesn't have any reference to the supplier's part number. There's a lot that needs to be done to make this whole supplier thing work well. Wouldn't it nice to ping a suppliers server and ask for current pricing and availability. In OS have a button you can click and tomorrow have a box of McMaster (hardware supplier in US) at your door step that's accurate.