Welcome to the Onshape forum! Ask questions and join in the discussions about everything Onshape.
First time visiting? Here are some places to start:- Looking for a certain topic? Check out the categories filter or use Search (upper right).
- Need support? Ask a question to our Community Support category.
- Please submit support tickets for bugs but you can request improvements in the Product Feedback category.
- Be respectful, on topic and if you see a problem, Flag it.
If you would like to contact our Community Manager personally, feel free to send a private message or an email.
Hole Tool & Chamfer Upgrade?
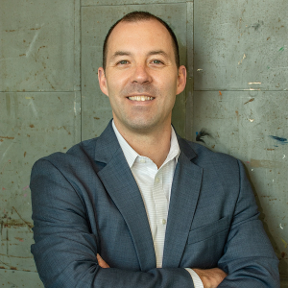
Would be nice to have a hole tool. Something with a standard library of diameters, and having toggles like counterbore, countersink, drill hole profile, etc.
Also, i'm sure it's being worked on but I haven't seen it mentioned yet - There needs to be more options for the chamfer, such as D X D, D1 X D2, Angle X D, etc.
Also, i'm sure it's being worked on but I haven't seen it mentioned yet - There needs to be more options for the chamfer, such as D X D, D1 X D2, Angle X D, etc.
Tagged:
6
Comments
I would add:
Threaded holes with (optional) modeled threads. Awesome for 3D printes prototypes.
Dries
Would also be cool to maybe have an extended library of "holes" for non-typical fasteners, like fully-crossed T-nut fasteners, heat-sink inserts, etc.
LearnOnshape facebook group
Linked[in]
**Note that the chain links have sections that are chamfered but not the entire link.
Cheers
@R3L4TIVITY Onshape does not have end-cap options for their chamfer feature (maybe one day) so there is no way to specify how the chamfer should start and stop.
To create the chamfer shape, use a swept cut.
You will have to use other geometry. A swept section of the tool that would create the chamfer plus revolve cuts of that same section at the end points will get this shape:
For the other details:
You won't be able to use existing geometry easily to get the sweep path; you'll have to offset the sweep path a variable distance from the edge yourself. It can be done...
But as an engineer I have ask; is this level of detail really needed?
Even if the tool were narrowly focussed to the single situation depicted above, representing a conical end-milling cutter following an arcuate path, then stopping, we're left with an infinite number of possible conical solutions, because the axial depth at which the tool happens to be set will change the location of the cut-revolve axis.
I can see some merit in being able to pick a vertex on an edge, or a plane intersecting an edge, and chamfer up to that entity. Essentially, the chamfer would be "hitting a brick wall"
The modeller could then sketch a cut-revolve on that wall.
However it's relatively easy to workaround within OnS current feature set, by temporarily splitting the body at those locations, chamfering, then re-merging.
It is sometimes problematic realistically modelling the results of 'form tool' milling operations, like a 'scowboat' keyway end, formed by withdrawing a bull-nosed endmilling cutter according to an arc-shaped (in side-view) toolpath.
Solidworks "Solid Sweep" should handle this, as well as the simpler chamfer termination tasks ... but last time I used it, it was unreliable.
@Traveler_Hauptman, the use of the specific detailing on the chain is so that the chain can be guided better onto the cogs as a mountain biker rushes down the hill bouncing around. Although there are chain guides that already do a good job, the chain still gets some flex and has potential to miss a tooth from that cog and jamming the chain guide, or derailleur as i found out, making it impossible for you to peddle forward.
You should also check the thread about loft. https://forum.onshape.com/discussion/341/loft