Welcome to the Onshape forum! Ask questions and join in the discussions about everything Onshape.
First time visiting? Here are some places to start:- Looking for a certain topic? Check out the categories filter or use Search (upper right).
- Need support? Ask a question to our Community Support category.
- Please submit support tickets for bugs but you can request improvements in the Product Feedback category.
- Be respectful, on topic and if you see a problem, Flag it.
If you would like to contact our Community Manager personally, feel free to send a private message or an email.
Can one move a part from one part studio to another within a document.
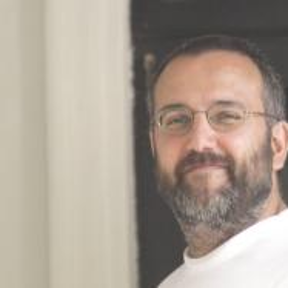
I am currently looking a remodelling a complete product in OS. I have all the parts and assemblies already modelled in SW and I think I can remodel it in OS with its current toolset. When I upload the SW STEP file they go into a new Part Studio which is fine. I would like to 'copy and paste' the chosen parts into a 'Part Studio' that I am creating from scratch. These pasted parts will act as the 'visual template' as I remodel them in OS from scratch and make Part Studios for each assembly that best use OS structures. I can't seem to do this. I could I suppose use the STEP part studio and then delete the imported parts. I think I have answered my question as a way to do it . Am I approaching this from the wrong angle?
However - is 'copy and paste' of parts from studio to studio a feature that is possible and worth having? I can imagine there will occasions when a lot of work has been done in a 'part studio' - driving sketches, parts etc and then there is a need to 'import' some outside data to assist in further modelling or defining new parts in the parts studio. How can this be achieved?
The reason for doing this is the product is made offsite and I think the manufacturer and I will solve alot of our communication problems using OS for this product rather than SW ( which is really beyond their skills, budget and patience ;-) ) so I think its worth remodelling from scratch rather than just using the STEP assembly import.
Regards
Jon
However - is 'copy and paste' of parts from studio to studio a feature that is possible and worth having? I can imagine there will occasions when a lot of work has been done in a 'part studio' - driving sketches, parts etc and then there is a need to 'import' some outside data to assist in further modelling or defining new parts in the parts studio. How can this be achieved?
The reason for doing this is the product is made offsite and I think the manufacturer and I will solve alot of our communication problems using OS for this product rather than SW ( which is really beyond their skills, budget and patience ;-) ) so I think its worth remodelling from scratch rather than just using the STEP assembly import.
Regards
Jon
www.naturalshelter.com https://www.linkedin.com/in/digitalnaturedesign
0
Best Answers
-
traveler_hauptman Member, OS Professional, Mentor, Developers Posts: 419 PRO
Your approach ("I could I suppose use the STEP part studio and then delete the imported parts") is the way to go right now. I'm pretty sure copying imported parts between part studios will be possible in the future. I'm guessing it's unlikely they will support copying partstudio parts between partstudios.
5 -
billy2 Member, OS Professional, Mentor, Developers, User Group Leader Posts: 2,100 PRO
Jonathon-
I tend to use parasolids binary because it's the smallest file size between step & parasolids. Both work fine. STEP is an international standard so there's nothing wrong with using it except for file size.
When I got started inside OS I did exactly what you are doing. Turns out I had to flip my own geometry as that function wasn't available when I imported my model. If you're coming from SW you'll probably want to flip the geometry and flatten everything into one partstudio (both check boxes checked).
This is where you and I depart in technique: I re-modeled on top of the imported geometry and you, created 2 documents.
I would define my sketch based on the underlying geometry but not tie to the underlying geometry and then would "U-use" the edges from the old geometry then break these "use" constraints after copying the geometry. This would give me accurate geometry that I could dimension and build references to. It's important not to tie anything to the imported geometry.
At the end I had one partstudio that had both the imported & new geometry inside of it. The last step was to delete the imported geometry which I did and nothing in the new geometry erred. Maybe I got lucky. The nice thing about OS is that when I delete a feature that has child references nothing gets absorbed and deleted. Children are never deleted inside OS. The worse that would happen is you would have to fix a broken reference. In SW, it would be a disaster because half your model would go away.
In your approach you have to measure then build, measure then build which isn't all that bad and it works.
I think my approach might be a little faster and less tedious. After a while you don't even think about what you're doing and you're on autopilot re-parameterizing a dumb solid.
re-parameterizing a dumb solid
I do this a lot and I find a lot of people doing it also. As a contractor I get invited into many companies to work on projects that have gone south. After looking at the models its no wonder why the project went south. At this time you have to decide if you want to proceed with a crappy parameterized solid or start over. 9:1 I'll start over. It sounds gruesome but it always pays in spades to start over with a dumb solid. How do you make a dumb solid in SW?
We're at a fork in the road and many people will want to move from SW to OS. Conventional wisdom says to wait till the next project to switch. I don't like this and I'll send a dumb solid and re-parameterize it in the new system. Why wait? It's really fast. OS still needs to clean some stuff up to help with this use pattern, but it's totally doable as it stands today.
Some people freak out when they open a part and there's only one imported feature. Some of us say 'yeah' I get to build it the way I want to and save a lot of time.
Here are some posts from when I imported geometry:
https://forum.onshape.com/discussion/38/imported-geometry#latest
https://forum.onshape.com/discussion/63/making-something-useful#latest
https://forum.onshape.com/discussion/70/geometry-completed#latest
https://forum.onshape.com/discussion/144/mate-connectors#latest
5
Answers
I tend to use parasolids binary because it's the smallest file size between step & parasolids. Both work fine. STEP is an international standard so there's nothing wrong with using it except for file size.
When I got started inside OS I did exactly what you are doing. Turns out I had to flip my own geometry as that function wasn't available when I imported my model. If you're coming from SW you'll probably want to flip the geometry and flatten everything into one partstudio (both check boxes checked).
This is where you and I depart in technique: I re-modeled on top of the imported geometry and you, created 2 documents.
I would define my sketch based on the underlying geometry but not tie to the underlying geometry and then would "U-use" the edges from the old geometry then break these "use" constraints after copying the geometry. This would give me accurate geometry that I could dimension and build references to. It's important not to tie anything to the imported geometry.
At the end I had one partstudio that had both the imported & new geometry inside of it. The last step was to delete the imported geometry which I did and nothing in the new geometry erred. Maybe I got lucky. The nice thing about OS is that when I delete a feature that has child references nothing gets absorbed and deleted. Children are never deleted inside OS. The worse that would happen is you would have to fix a broken reference. In SW, it would be a disaster because half your model would go away.
In your approach you have to measure then build, measure then build which isn't all that bad and it works.
I think my approach might be a little faster and less tedious. After a while you don't even think about what you're doing and you're on autopilot re-parameterizing a dumb solid.
re-parameterizing a dumb solid
I do this a lot and I find a lot of people doing it also. As a contractor I get invited into many companies to work on projects that have gone south. After looking at the models its no wonder why the project went south. At this time you have to decide if you want to proceed with a crappy parameterized solid or start over. 9:1 I'll start over. It sounds gruesome but it always pays in spades to start over with a dumb solid. How do you make a dumb solid in SW?
We're at a fork in the road and many people will want to move from SW to OS. Conventional wisdom says to wait till the next project to switch. I don't like this and I'll send a dumb solid and re-parameterize it in the new system. Why wait? It's really fast. OS still needs to clean some stuff up to help with this use pattern, but it's totally doable as it stands today.
Some people freak out when they open a part and there's only one imported feature. Some of us say 'yeah' I get to build it the way I want to and save a lot of time.
Here are some posts from when I imported geometry:
https://forum.onshape.com/discussion/38/imported-geometry#latest
https://forum.onshape.com/discussion/63/making-something-useful#latest
https://forum.onshape.com/discussion/70/geometry-completed#latest
https://forum.onshape.com/discussion/144/mate-connectors#latest
Jon
They're going to have to support partstudio into partstudio. What if I download a bolt and want to add it to a partstudio? They have to merge partstudios, sooner than later, hopefully sooner.
I find OS to be a cleaned up version of SW. As far as creating geometry I prefer OS to SW. I don't this will take long for you to agree.
I'm interested in your assembly approach. This will take some thought.
Each partstudio is a sequence of features that generates a group of parts. It's possible to create a part that has a clean feature history, one that does not depend on any features of the other parts, and thus it would be technically possible to copy this kind of part from one studio to another. I do hope that Onshape supports this (Your bolt for instance, with configurations for all the sizes I need, could be one of many 'seed' parts for a studio). However, in general there are going to be multiple parts in a partstudio and extracting just one part for copying will not be possible in many cases.
In many cases inserting the geometry of a part via reference (which I expect to be available reasonably soon) will be the preferred way. If you import via reference then you are not repeating features; which reduces the places you need to look when coming into a project cold.
HWM-Water Ltd
https://cad.onshape.com/help/Content/derived.htm